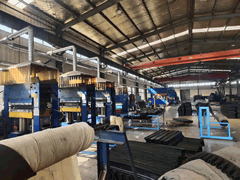
1、厚度在3.1—6.0 mm的胶片厚度公差是+0.2,-0.3 mm。
2、胶片宽度在800-2400 mm的胶片宽度公差为+15,-5mm。
3、在用四辊压延机压延普通覆盖胶时,压延机1#辊筒温度应在50-60℃范围内。
4、胶片表面要求光滑,无胶眼和自硫胶料,压延胶片经冷却后,其最高温度不得超过 40℃。
5、胶片检查时发现长20mm×10mm以下的气泡可以算合格品。
6、压延棉帆布最高车速不大于 30m/分。
7、标准宽度为650mm的输送带,其外层纵向接头不允许有。
8、输送带两头接头布不短于2米,外层接头不短于3米。
9、布层横向接头应与输送带的中心线呈45~70°角。
10、横向接头在不同布层之间的距离应不小于3米,在同一布层之间的距离应不小于5米。
11、在冷压、硫化整个作业过程中,均应施加张力,只允许在牵引带子装锅时解除张力。
12、宽度为1500mm的胶片,胶片厚度为4mm,每卷长度为70m,是符合规定的。
13、全乙丙耐热(150℃)带覆盖胶厚度要求为2mm,实际测量1.9mm是可用的。
14、每100米长度输送带,其外层布每层应不超过一个横向接头,其内层布每层不超过两个横向接头。
15、覆盖胶片厚度,应符合标准规定,要经常测量,贴合时不得受伸,大的胶折子不准有,不得有缺胶,胶片搭接必须贴牢。
16、胶料严格按先后顺序使用,看清胶号避免错用,混炼胶停放时间不少于 4小时,最长时间不超过 144 小时。
17、已上车的钢丝绳,因故不能在72小时内继续冷压硫化时,应及时覆盖。这么做是为了防止钢丝绳 沾上灰尘 或 氧化 。
18、在钢丝绳接头时两边部各 3 根钢丝绳不允许有接头。
19、钢丝绳接头根数不得超过总根数的 5% 。
20、带胚两侧厚度偏差不得大于 1mm 。
21、造粒过程应随时观察加料筒内粉料下移情况,防止膨料。
停机时将剩余粉料放出,装袋封严,卸下机头认真清理,将机筒内剩余料挤出后再重新装上机头。
注意检查储槽内粒料的温度,防止结团。
22、造粒挤出机工艺要求:
螺杆转速:40-60转/分
机头温度:135±5℃
机身温度:1#区:115±5℃;2区#:125±5℃;3#区:130±5℃;4区#:135±5℃
23、挤贴盖胶操作要点
(1)带芯贴胶面,两台挤出机同事以低速启动,喂料,调整出片情况(出片要求两边稍快,中级稍慢,显︻型,厚度要均匀)。
(2)待带芯达到贴胶位置时将两台挤出机合拢,用螺栓绞紧,开始挤贴盖胶,要求两侧带体厚度偏差小于0.2mm,并同时将压合辊冷却水打开。
(3)在挤胶过程中,应注意调整挤出速度,达到产品要求,同时随时调整调偏块,以保两侧边胶规整一致,边胶宽度控制在3-6mm。
(4)挤出过程中,随时注意上料情况,以保证挤出机的供料并防止膨料。
(5)挤出过程中,应随时注意带芯运行中心情况,防止跑偏。
(6)挤出过程中应随时注意观察挤出机及模具各部温度变化并及时加以调整。
(7)挤出过程中出现异常情况,应找技术人员处理。
(8)遇到临时故障,运行中无法处理时应立即停机,停机时应停止加热并打开塑化箱散热。
(9)停止生产(生产活动终止时)全部设备停止加热,两台挤出机同时离开,卸下模具后开机喂进少量粒料将机筒内的余料挤出干净,模具清理后上油装好,清理模具过程中严禁使用铁器。
(10)挤出的边角料,打片料,机头料要注意清理,不得沾染杂质,沾水后应晾干,妥善保管,经粉碎后按1:4的比例掺用(具体掺用比例按技术部的通知执行)。
(11)同批次或同规格连续化生产120小时后,应停机清理挤出机头及挤出模具一次,防止机头及挤出模具具有堵膛及糊料,造成挤出量不均现象发生。
(12)生产高级别带或覆盖胶厚度大于1.0mmPVC/PVG带时,必须重新上硫化平板进行硫化冷却处理,防止带胚塑化程度不够和附着力不符合标准要求。硫化条件:155℃X10min、冷却至80℃下锅。